overview
Our full-featured automatic coil winders may be the only mandrel winding machine you’ll ever need! This model is capable of repeating the coiling cycle by automatically winding, unloading, cutting the coil, and starting the cycle over again. This model produces high-quality coils for guidewire and other specialized medical devices and has proven it’s accuracy by measuring its coil quality over and over again.
RothGreaves has developed our proprietary EasyWind software; this custom software was created for multi-pitch, multi-segment, multi-speed coil profiling. This is the most advanced software on the market today. EasyWind advanced features have recipe development and full security level control. All of our machines are operated by a CNC servo controller for extreme accuracy and reliability.
*Cutting Station sold separately
coil winder features
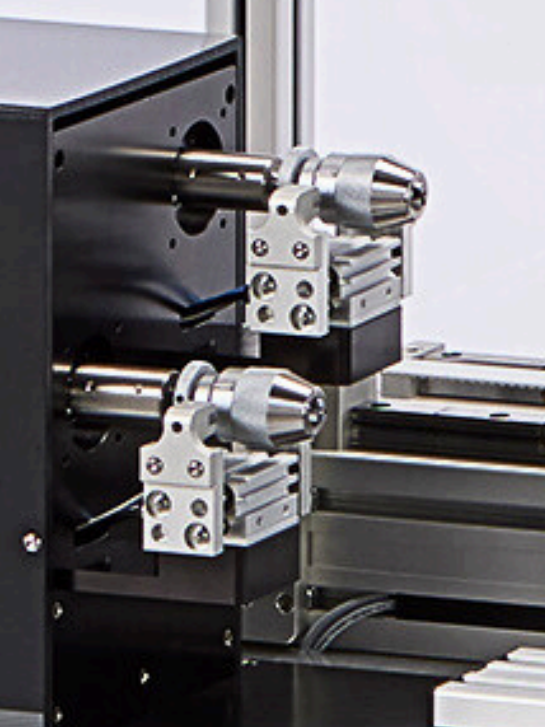
The Automatic’s collet chucks are specially designed for automatic operation, available in a range of sizes, and are interchangeable
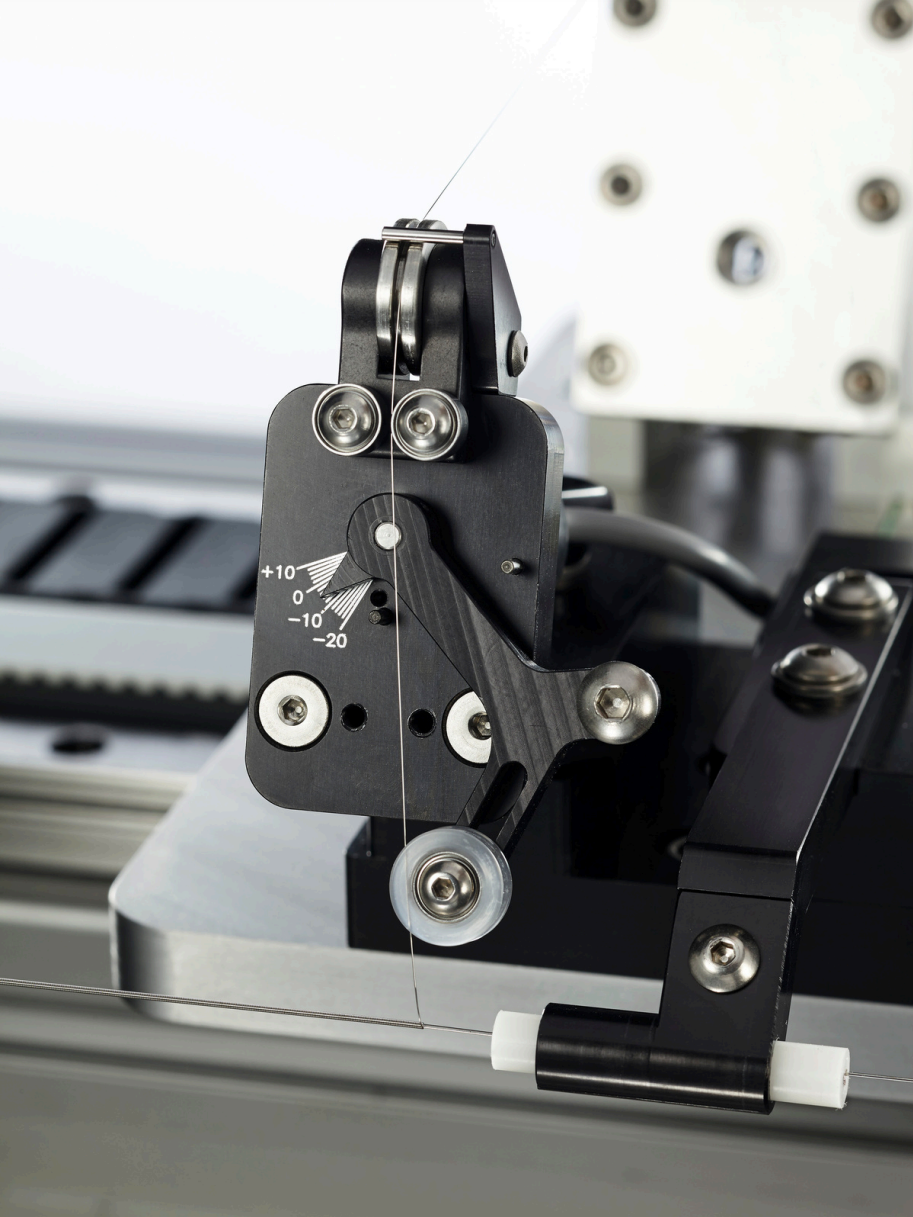
The angle control compensator is designed to fit directly onto our quick change tooling base
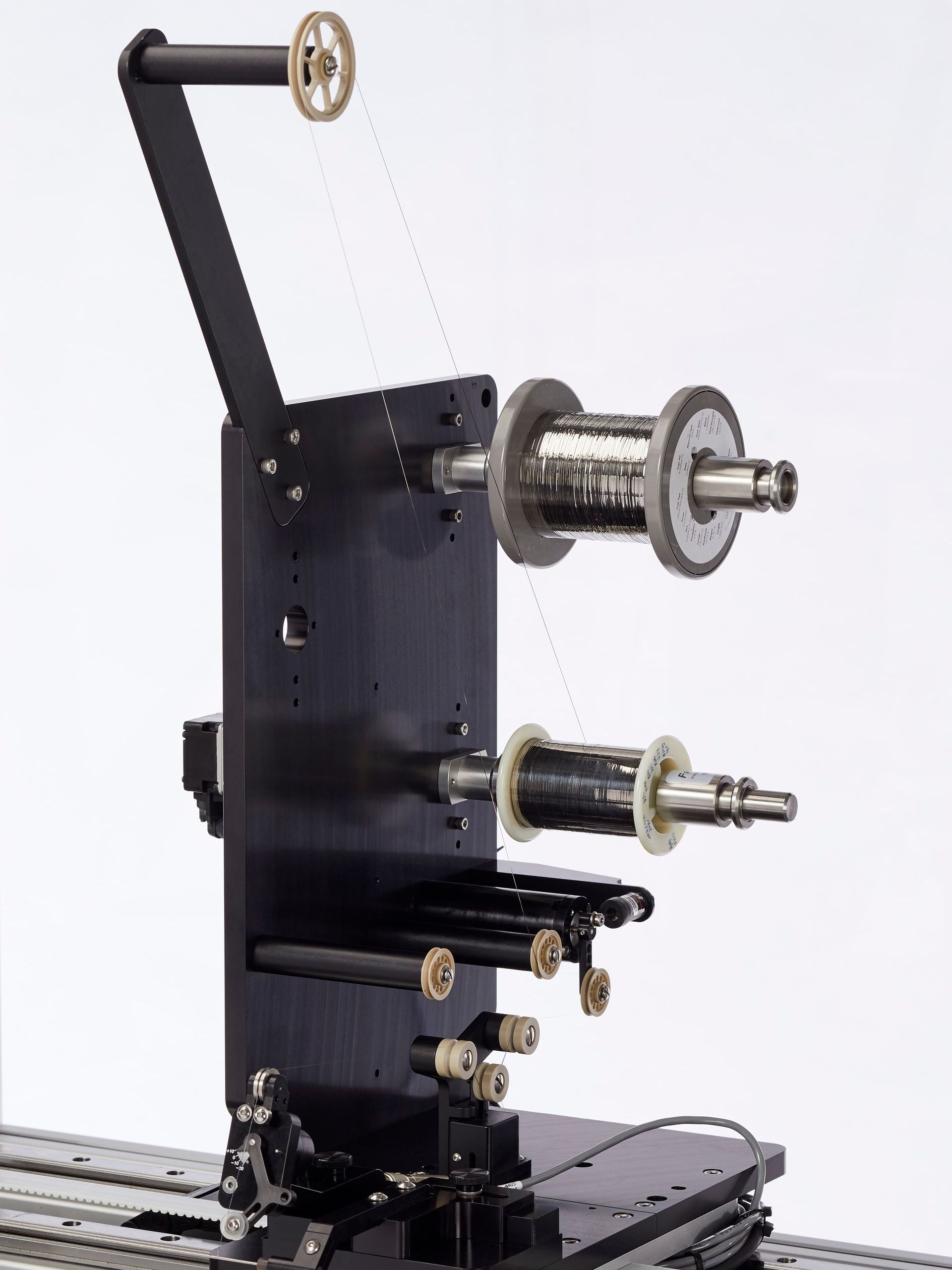
The payout rack is designed for precise tensioning so your diameter requirement is seen throughout the entire coil.
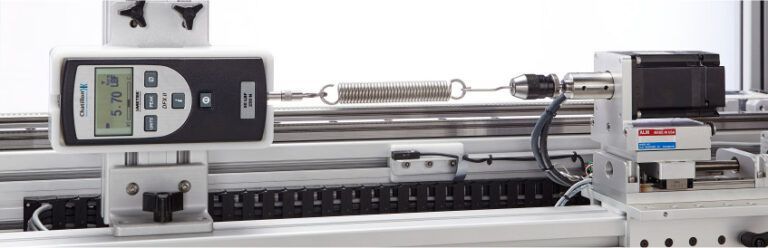
Automatic Arbor Tension allows the operator to establish an exact arbor tension for more precise winding. Arbor Tension Calibration Instrument Package is sold separately
5000 Series Automatic Coil Winder specifications
- CE CERTIFIED
- Dimensions: 135" L x 35" W x 38" H
- Chuck-to-chuck length: 96"
- Power requirements: 208-240 VAC, Single Phase, 50/60 Hz, 10 Amp
- Pneumatic requirements: 80 psi @ 3.0 cfm
- Servo motors/Drive amplifiers: Spindles (2) – 400 watt, Carriage (1) – 750 watt
- Winding speed max: 6000 rpm
- Controller type: CNC multi-axis servo controller
- Operating System: Microsoft Windows 10
- Manual jog controller: Pendant with joystick operation all axis
- Operating Software: EasyWind™
- Interface: 17" touch screen monitor and trackball keyboard
- Wire tensioning: Electronic
- Arbor tensioning: Pneumatic with or without feedback
- Tailstock Chuck sizes: 1/16", 1/8", ¼" (option)
- Headstock Collet sizes: 0.010" to 0.180" (option)
- Collet sizes: 0.036" diameter to 0.500" diameter
- Safety features: Light curtain with surround or door with surround
GLOSSARY OF Coil Winder TERMS
Coil Winder FAQs
What types of coil winders do you offer?
We have two basic types of machines:
- Our manual load (and unload) machine requires an operator to load the mandrel into the chucks, secure the wire, start the cycle, then unload the mandrel or coil. The load and unload process typically takes less then a minute for a trained operator. Wire change over takes about two minutes.
- The automatic machines take roughly five minutes to start up but will then run unattended until asked to stop or the wire spool empties. Change-over to new wire takes about five minutes.
Can you customize a coil winder?
Yes, with added features and tooling.
What makes the RothGreaves Coil Winder the industry best?
Our machines with standard equipment, offer more capabilities than any other mandrel winding machine available. Our wire angle compensation is the most robust in the industry and our force feedback arbor tension is very accurate. And our attention to details differentiates our machines from our competitors’.
Do you provide a maintenance list with your Winders?
A recommended maintenance list is included in the operator’s manual but generally, these machines require very little in the way of maintenance. Some cleaning and lubrication is about all that is needed.
What models are available?
Our standard coil winders include the 4000 Manual, 4500 Mini, 4800 Bunk Bed, 5000 Automatic, 6000 Side Winder, and 8000 Multi-Filar. If you need a custom coil winder please contact us.
Are RothGreaves Winders CE Marked?
Yes. RGA designs and constructs all our machines for full CE compliance and offer different types of safety features from simple guarding to light curtain enclosures.
What direction does the EasyWind™ software provide?
The winder can coil left-hand or right-hand coils. It also is multi-directional. The operations manual offers detail in how to use the software for both left- and right-hand coils. The carriage can coil in both directions.
What is the maximum traverse speed?
Maximum traverse speed is related to the pitch but the maximum carriage speed is 15 inches per second. (This rate is usually only used during carriage returns.)
What is the maximum spindle speed?
6000 rpm
What is the payout or wire angle that can be used?
We can set up for a 25 degree back angle and forward angle (open pitch condition).
What are the maximum/minimum pitch settings?
– Minimum programmable pitch = 0.0001” per rev.
– Maximum programmable pitch = 10.000” per rev.
– Tolerance for control + 0.0002”
What is the range of wire that can be wound?
The smallest wire that customers are winding is a 0.0006” diameter platinum and the largest known is 0.035” diameter stainless. They will also wind profile wire; rectangle, square, oval.
What is the amount or range of wire tension?
This is dependent on the size of the torque controller desired. There are ranges of shaft torque for the wire spool that span:
- 0-3 oz-in.
- 0-11 oz-in.
- 0-35 oz-in.
- 0-85 oz-in.
- 0-140 oz-in.
This ranges in grams at point of delivery from as small as 5 grams. The tolerance is size dependent, as the range increases, so does the tolerance.
What is the length of arbor or mandrel required?
The tail-stock is fully adjustable just as it is on a lathe, so there is no minimum length. The longest wind length winder we have manufactured was 450cm.
What are the smallest/largest arbor sizes that can be used?
Our standard models go down to a 0.001” chuck capacity and can go up to 0.500”. If required, we can go larger.
What is the method of tensioning the arbor or mandrel?
Two sizes of pneumatic tensioning are available 0-20 lbs and a 0-80 lbs. These are adjusted with air pressure via a regulator mounted on the tail-stock. A high end force feedback tensioning has ranges from 0-5 lbs up to 0-50 lbs, the control is via the coil recipe and the value can be set in grams or pounds.
Do you have an operations manual?
Yes, copies of our manuals are available upon request.
What do you offer for training?
Training at our facility is available at no charge for companies that purchase a machine. We also offer on-site training for a fee. The training is for both engineers and operators.